Saw Servicing and Repair
Addison’s team of service engineers are based all over the UK and undergo extensive training programs to ensure they delivery the best possible service. Our goal is to assist in keeping your production at optimum levels through saw servicing and repair, no matter where you bought your machine.
Industrial Machine Servicing
-
Time Based Servicing
Is your cutting machinery due an annual service? If you prefer to book your saw servicing when you think you need it, we will do our best to get an engineer out to you around your preferred date. Standard call out costs apply, and while we aim to complete servicing in one visit, further visits may be necessary to complete the job.
HSE guidelines state that work equipment must be ‘maintained in an efficient state, in efficient order and in good repair’ Work equipment and machinery (hse.gov.uk) and we don’t want our customers to get caught short, so we do generally recommend all of our machinery is serviced at least once a year or every 2,000 working hours, which ever comes first, to keep your machinery operating safely and in top working order. This can be discussed further with a member of staff who will go through your unique working environment and advise on the most suitable timeframe.
-
Preventative Maintenance Agreements (PMA)
Designed to help significantly reduce downtime and cost, and it’s proven to do just that for all company sizes, small or large. The PMA is a scheduled visit agreement for saw servicing.
We schedule 1 visit per year for a single shift operation (2,000 working hours) at a fixed cost which will be invoiced upon completion. All machines should be serviced regularly to pick up on any possible future problems, and saws are no exception. We also understand that downtime can be extremely costly, so the PMA aims to eliminate the threat of sawing machines and machining centres breaking down – keeping your workshop or factory running as smoothly as possible. The PMA also comes with a 15% discount on spare parts when they are needed along with labour time, leading to even bigger savings in the long run. Contact the service department on 01384 264 950 to find out more.
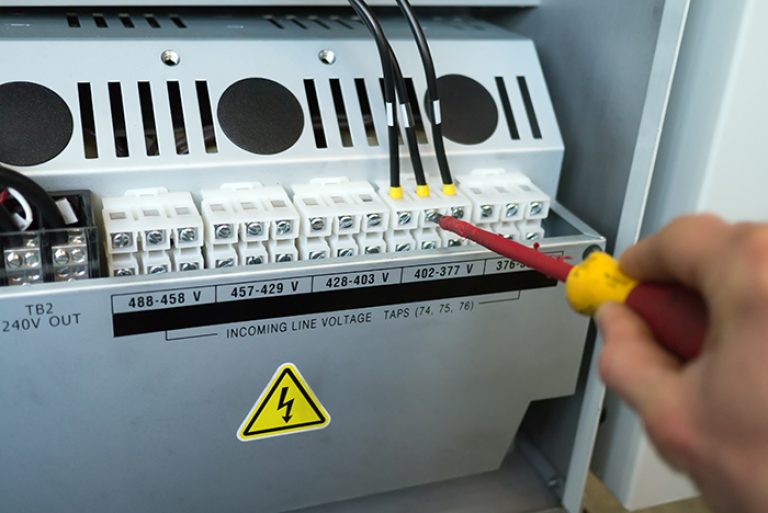
Machine Repair
When a saw, machining center or tube bender goes down, you need the problem to be fixed ASAP. Here at Addison’s, we have expert service engineers stationed nationwide, who aim to be with you asap and with the parts you need (a second visit may be necessary if the problem requires it).
What machines do we repair?
We aren’t limited to fixing the brands we offer, our engineering team can diagnose and repair most brands of band saw, chop saw, aluminium saw and machining center available in the UK. Our team can also source spare parts directly from manufacturers to fit during the saw repair, ensuring you only get the best parts for your machine.
Machine Commissioning & Installation
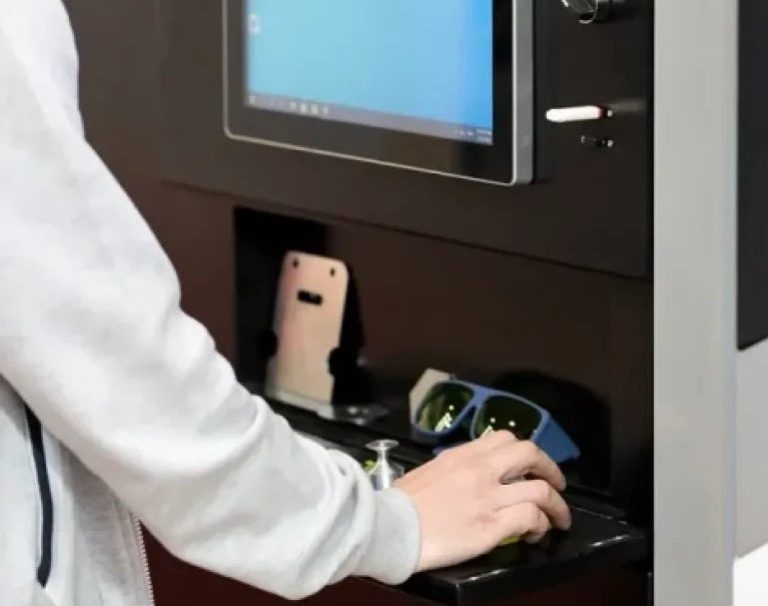
Addison are dedicated to ensuring that your cutting machine becomes a valuable addition to your operations right from the moment it arrives at your facility. Our commitment to you extends beyond delivery – we are here to commission, install, and provide the initial training that will empower your team to to get the most out of your new industrial equipment.
Our comprehensive commissioning program consists of the following key elements:
- Machine Set-Up and Blade/Tooling Changes: Our experts will guide your operators through the critical process of machine set-up and assist in efficient blade or tooling changes, tailored to your specific job requirements.
- Machine Programming (if applicable): If your cutting machine requires programming, we ensure your team masters this vital aspect, enabling precise control over your equipment.
- General Machine Use: We ensure that your operators are well-versed in the machine’s functions and capabilities.
- Health and Safety Best Practices: Safety is paramount, and our training includes essential guidelines and practices to ensure the well-being of your operators.
- Total Productive Maintenance: We emphasize the concept of Total Productive Maintenance, an approach to maintenance that promotes continuous improvement. Your operators will be equipped with the skills to conduct proactive and preventative maintenance, covering daily, weekly, and monthly checks. This empowers your team to maximize machine effectiveness, reduce downtime, and enhance operational efficiency.
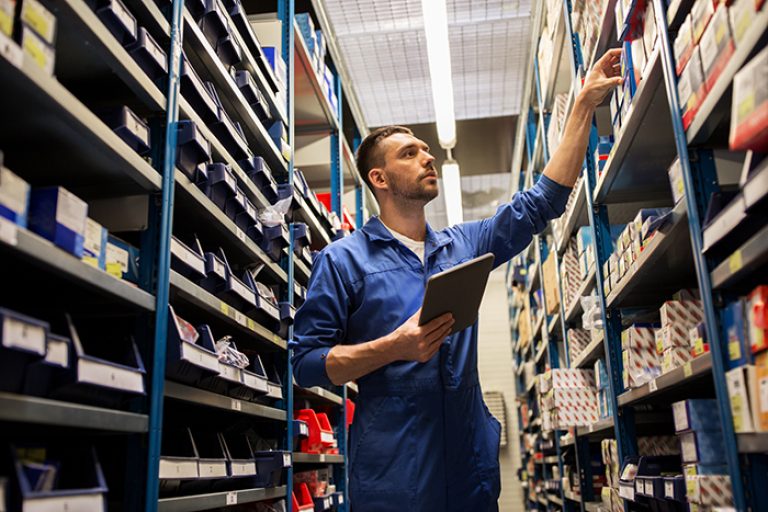
Spare Parts
We stock thousands of spare parts and can supply many more for most makes and models of cutting machinery. Furthermore, stocked items are available for collection or next day delivery within the UK.
Address
Addison Saws Ltd Attwood Street Lye Stourbridge
DY9 8RU
Phone
Fax